Enhancing Production Efficiency with Silicone Injection Molding Machines
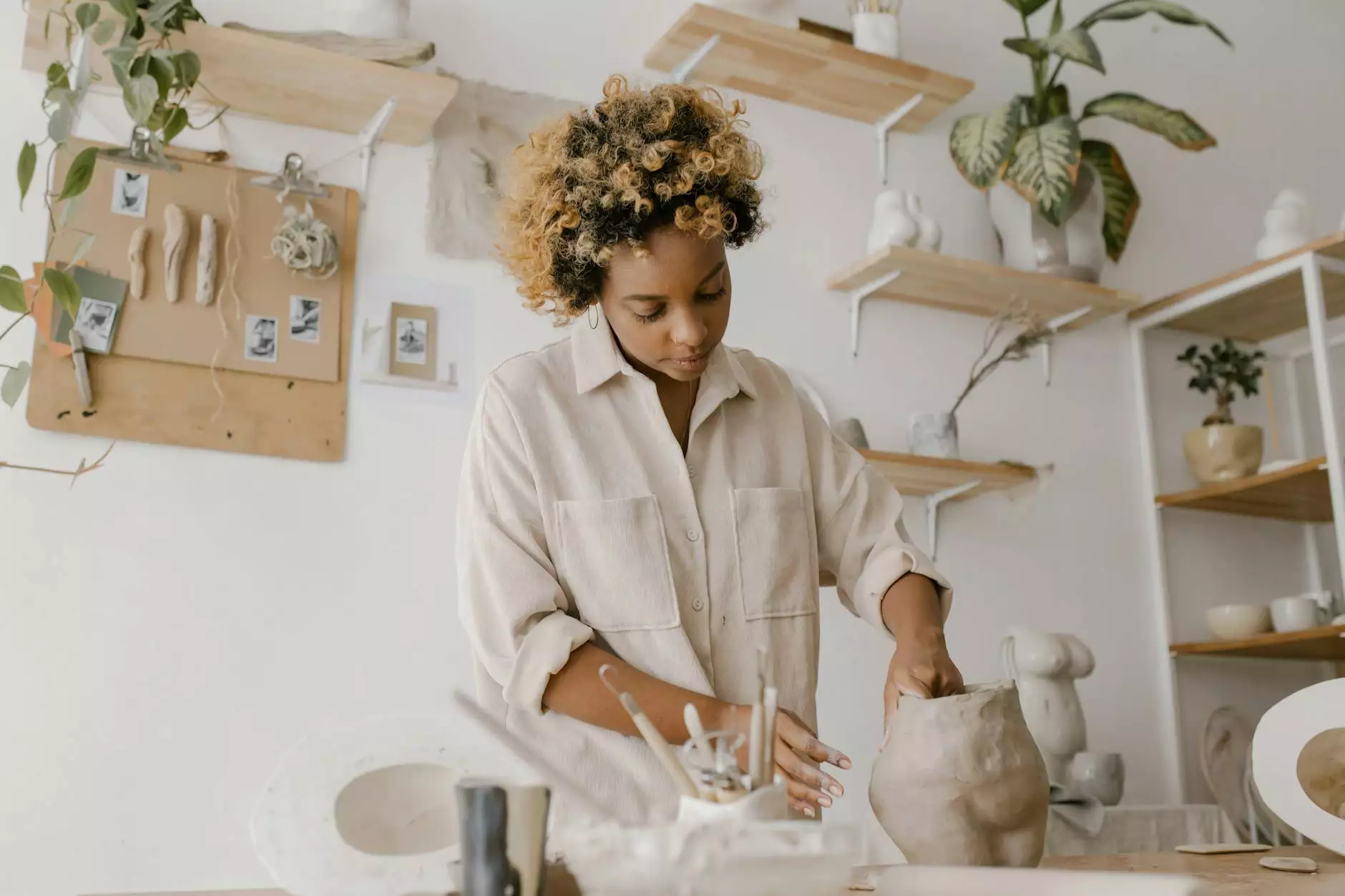
In the rapidly evolving landscape of manufacturing, the demand for precision and efficiency has never been higher. A significant part of this evolution lies in the adoption of advanced technologies. One cornerstone technology in this regard is the silicone injection molding machine. This article will delve into the workings, advantages, and applications of silicone injection molding machines in the context of the Electronics and Medical Supplies industries.
The Fundamentals of Silicone Injection Molding Machines
Silicone injection molding is a process used to create silicone rubber products through the injection of liquid silicone into a mold. The versatility of silicone allows for extensive applications due to its inherent properties such as flexibility, durability, and heat resistance. Here, we will examine how silicone injection molding machines operate and their components.
Understanding the Process
The silicone injection molding process involves several stages:
- Molding Preparation: The machine is prepared by installing necessary molds tailored to the product specifications.
- Material Loading: Liquid silicone is loaded into the injection barrel of the machine.
- Injection: The machine injects the liquid silicone into the mold cavity under high pressure.
- Curing: Once injected, the silicone undergoes a curing process where it solidifies and gains its final shape.
- Demolding: After curing, the mold is opened, and the finished product is ejected.
Advantages of Using Silicone Injection Molding Machines
Investing in a silicone injection molding machine offers numerous advantages that can lead to substantial improvements in production processes across various sectors, particularly in electronics and medical supplies.
1. High Precision and Quality Control
The silicone injection molding machine delivers precise results with minimal variation in dimensions, ensuring that each product meets strict specifications. This high level of accuracy is critical in medical supplies where product imperfections could have significant consequences.
2. Efficiency and Reduced Cycle Times
One of the most compelling reasons to adopt silicone injection molding is the production speed. These machines can operate at high speeds, significantly reducing cycle times and maximizing output. Faster production translates to higher profitability, allowing businesses to meet increasing market demands swiftly.
3. Versatility in Design
Silicone injection molding machines can create complex shapes and intricate designs unattainable by other manufacturing methods. This versatility enables manufacturers to experiment with innovative designs, catering to specific needs in the electronics sector and medical applications.
4. Cost-Effectiveness
While the initial investment in a silicone injection molding machine can be substantial, the long-term savings on labor, material waste, and production time make it a cost-effective solution. Moreover, the durability of silicone products means that the end-users benefit from longer-lasting items, reducing the need for replacements and returns.
Applications of Silicone Injection Molding Machines
The applications of silicone injection molding machines are vast, impacting several sectors, especially Electronics and Medical Supplies. Here’s a closer look at how these machines are utilized in different fields:
Electronics
In the electronics industry, silicone is commonly used for:
- Insulation components: Silicone provides excellent electrical insulation properties.
- Encapsulation materials: Protecting electronic components from environmental factors.
- Keypads and buttons: Silicone’s flexibility allows for comfortable and durable user interfaces.
Medical Supplies
The medical field benefits greatly from silicone injection molding machines, particularly in the following areas:
- Medical devices: Production of precision parts for devices such as surgical instruments and diagnostic tools.
- Healthcare products: Manufacturing silicone-based products like catheters, gaskets, and seals that need excellent biocompatibility.
- Wound care and dressings: Silicone’s gentle nature is beneficial for skin applications, minimizing irritation.
Choosing the Right Silicone Injection Molding Machine
Selecting the right silicone injection molding machine is crucial for optimizing your production line. Here are some factors to consider:
1. Capacity and Size
Determine the required production volume and choose a machine that can handle it efficiently. Larger machines may be necessary for high-volume production but consider space constraints in your facility.
2. Control Systems
Modern machines come with advanced control systems that help monitor and adjust the injection process. Look for machines with user-friendly interfaces and automation features that streamline operations.
3. Energy Efficiency
Opt for machines that prioritize energy efficiency to reduce operational costs. Energy-efficient machines not only save costs but also contribute to a more sustainable manufacturing process.
4. Support and Maintenance
Consider the level of support and maintenance services offered by manufacturers. Choosing a supplier that provides reliable support can reduce downtime and keep your production line running smoothly.
Future Trends in Silicone Injection Molding
The landscape of silicone injection molding is poised for transformation due to technological advancements. Here are some trends to watch:
1. Integration of Smart Technologies
With the rise of Industry 4.0, manufacturers are integrating smart technologies in silicone injection molding machines to enhance connectivity and control. This includes IoT-enabled devices for real-time monitoring and predictive maintenance.
2. Sustainable Manufacturing
Sustainability is becoming a key focus in manufacturing. Future silicone injection molding machines will likely incorporate eco-friendly practices such as the use of recycled materials and reduced energy consumption.
3. Advanced Materials
There is growing interest in developing new silicone compounds that offer superior properties such as increased elasticity and temperature resistance, which will further expand the possibilities of silicone injection molding.
Conclusion
The silicone injection molding machine represents a significant advancement in the manufacturing process, particularly for industries like electronics and medical supplies that demand high-quality, precision-engineered products. By understanding the benefits and applications, businesses can leverage these machines to enhance their production capabilities, optimize their processes, and stay competitive in a fast-paced market.
As technology continues to evolve, the future of silicone injection molding looks bright, promising innovations that will redefine manufacturing standards. Investing in silicone injection molding machines is not merely a choice; it's a strategic move towards improving efficiency, reliability, and product quality.